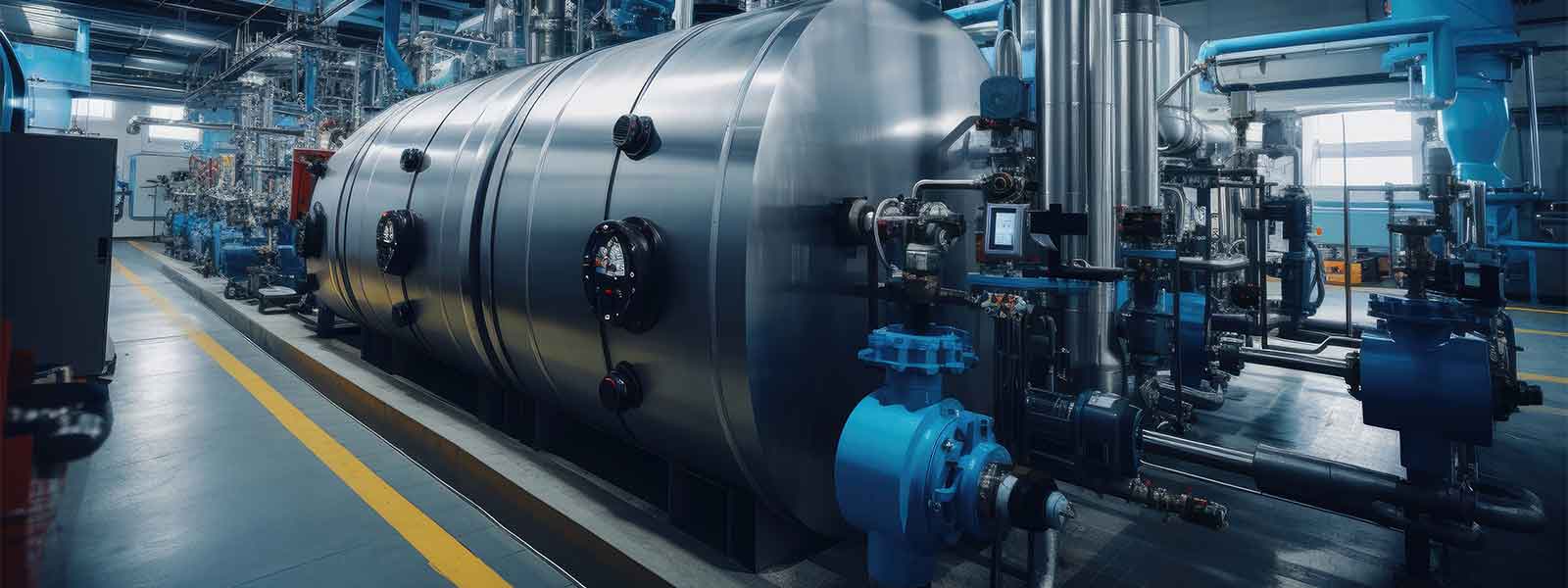
Reverse Osmosis (RO)
As abundant as our planet’s water supply seems to be, only 2 percent of Earth’s water is fresh water; and less than 1 percent is actually available for human use. With the growing population and consequently, the increasing demand for potable water and water for industrial use, the value placed on water is ever-rising – it’s easy to see why water is now being labeled as “the oil of the 21st century.” Therefore, the implementation of membrane processes for the production of “pure” water from fresh water and seawater has increased dramatically.
Prior to the last several years, Reverse Osmosis (RO) and other membrane processes for large-scale applications in potable water production, and in process and wastewater systems, were perceived to be merely experimental and they were very expensive. In recent years however, membrane technology has seen extensive advancements; in which, have improved the performance and extended the life expectancy of these systems. These advancements, particularly in reverse osmosis systems, have made it a cost-effective application for the production of “pure” water for industrial process water and potable water for consumption.
As with any industrial system where water is the hub of the operational wheel, the biotic and abiotic constituents in the available water for process requires treatment to prevent fouling. In RO systems, membrane fouling can come from solids (silt, iron oxides, and manganese oxides), scaling due to dissolved salts, and microbiological organisms. Membrane feedwater should be relatively free from colloidal particulates. But often, pretreatment is inadequate and/or ineffective, and chemical dispersants must be used to prevent particulate fouling. Fouling due to dissolved salts concentrations usually occurs in the form of calcium carbonate (CaCO3) and calcium sulfate (CaSO4). However, silica, barium and strontium salts are also common in membrane deposits. In order to control scale formation, deposit control agents must be applied. In regard to microbiological fouling, most RO membranes can be properly maintained by the use of chlorine or other oxidizing biocides. However, polyacrylamide membranes are susceptible to chemical oxidation. In this case, nonoxidizing antimicrobials and biodispersants should be used to prevent microbiological fouling.
Bio-Source is the largest distributor for BWA Water Additives in the U.S. Our product line for reverse osmosis systems consists of BWA’s Flocon® Membrane Solutions. Collectively, Flocon® membrane solutions are not affected by chlorine or other oxidizing biocides under normal conditions of use. These products may be used in systems using chlorine and sodium metabisulphite. Also, all Flocon® products are certified to ANSI/NSF Standard 60 for use in reverse osmosis systems producing potable water.
An outline of our solutions for reverse osmosis membrane treatment is listed below.
Flocon® 135
Antiscalant for Reverse Osmosis Systems: An aqueous solution of a specialized phosphinocarboxylic acid. It is highly effective in controlling the deposition of inorganic scale forming salts on membrane surfaces. This product offers excellent control of carbonate and sulphate scales, and is compatible with all major membranes. It is also a dispersant, and is iron tolerant.
Flocon® 190
Antiscalant for Reverse Osmosis Systems: An aqueous solution of organic phosphonate that is highly effective in controlling the deposition of inorganic scale forming salts on membrane surfaces. It exhibits excellent control of carbonate and sulphate scales, will not adversely interact with polymeric coagulant aids, and is compatible with all major membranes.
Flocon® 260
Premium Antiscalant and Antifoulant for Membrane Systems: An aqueous solution of a specialized polycarboxylic acid that serves as a dispersant, and is highly effective in controlling the deposition of inorganic scale forming salts and particulate fouling on membrane surfaces. It is an excellent control of carbonate, sulphate and fluoride scales, it effectively controls both soluble and insoluble iron, and it is effective against silica fouling. It is also compatible with all major membranes.
Flocon® 885
Biodegradable and Phosphorus Free Antiscalant for Reverse Osmosis Systems: This product contains no Phosphorus (P) and is a biodegradable antiscalant designed to control a range of inorganic deposits commonly occurring on RO membranes. It is an excellent scale inhibitor for Calcium Carbonate and Barium Sulphate; and it is considered to be a good inhibitor of Calcium and Strontium Sulphate, and Calcium Fluoride. Flocon® 885 enables reverse osmosis facilities to easily comply with effluent discharge restrictions, thereby offering an environmentally friendly solution. By containing no P, and biodegrading quickly in the environment, it is a sound membrane treatment solution designed to help maintain the vital integrity of our precious ecosystems. *Approved Reverse Osmosis Chemical in Florida. *Approved Reverse Osmosis Chemical in North American Great Lakes.
Flocon® Plus N
Antiscalant for Reverse Osmosis Systems: This scale inhibitor is a high-performance liquid product, and is highly effective in controlling the deposition of inorganic scale forming salts on seawater membrane units (SWRO). Specialized for Seawater Reverse Osmosis Desalination systems, this product exhibits excellent control of carbonate and sulphate scales, and it is compatible with all major membranes.
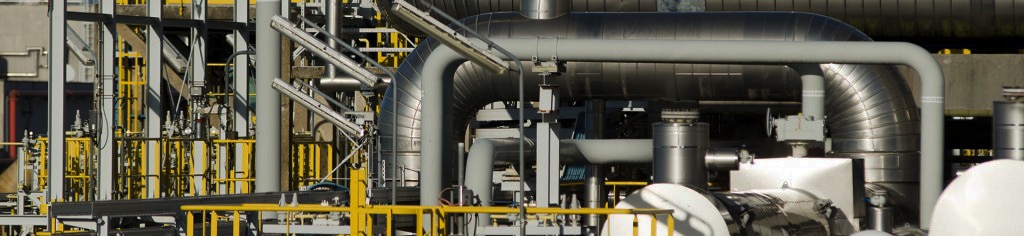
Get Free Consultation With Us.
Don’t Hesitate to Contact Us!